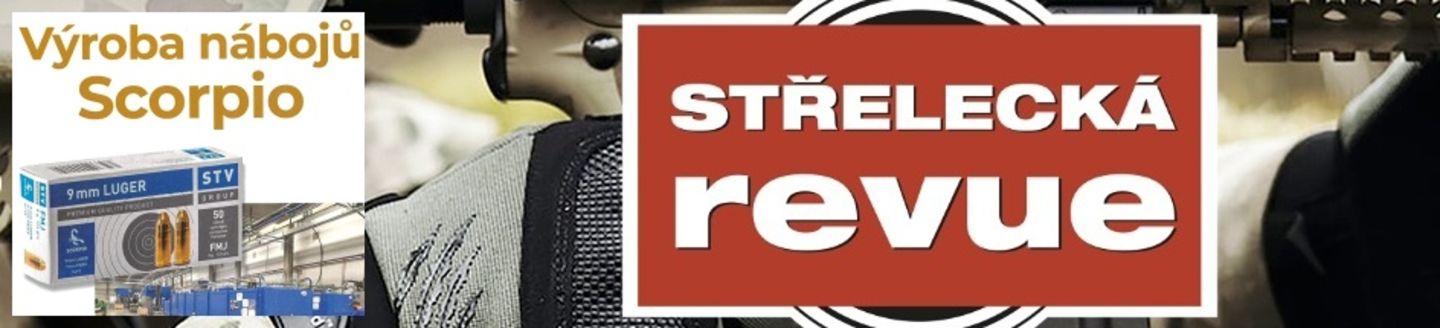
Production of Scorpio cartridges (article in Střelecké revue 3/2024)
Střelecká revue magazine published a report from our sister company STV Technology about the production of small calibre ammunition.
Scorpio small caliber ammunition production
Relatively recently, the production of small-caliber ammunition, which is mainly intended for the civilian market and mostly for export, was established in the premises of Poličské strojírny belonging to the STV Group. We were curious how the production is going and what are the plans for the future. We saw for ourselves the quality of the ammunition produced here. We found out that the production of both 9 mm Luger and 223 Rem / 5.56 x 45 mm cartridges in Polička is top-notch, and more positive experiences are coming.
The beginnings of production and the present
The Polička site, which was built in 1920 as the main capacity for the production of artillery ammunition for the Czechoslovak army, was fully controlled by the parent company STV Invest in 2015. The very next year, the decision was made to produce its own small-caliber ammunition in the subsidiary STV Technology, established for this purpose in 2016.
Production was initially carried out on very old machinery, which did not meet the current requirements for quality, economy of operation, quantity produced, and corresponding productivity. Everything was difficult and slow. However, in 2017, the first contracts were signed for the delivery of new technological equipment designed to produce 9 mm Luger cartridges with full metal jacket (FMJ) 8 g bullets. In 2021, new contracts were signed with suppliers of machinery designed to increase production capacity for 9 mm Luger cartridges, both the existing type with the FMJ 8 g projectile and to expand the production range to include cartridges with the FMJ 7.5 g and TFMJ 8 g projectiles. These machines are already installed and producing the ammunition.
Also in 2021, machinery was ordered for the production of 223 Remington rounds with a 3.56g FMJ round. The second half of 2023 was devoted to commissioning of the delivered technological units, semi-operational production, product testing and implementation of production and testing standards for products that were completely new to STV Technology. In the second half of 2023, production versions of the 9 x 19 mm NATO FMJ 8 g cartridge and the 223 Rem cartridge (which can also be referred to as the 5.56 x 45 mm M193) were introduced into the standard production and sales range.
In Polička, therefore, only 9 mm Luger cartridges in the aforementioned bullet variants and 223 Rem cartridges are produced so far, especially with a proprietary FMJ bullet weighing 3.5 g (55 grs), corresponding to the original American M193. Both cartridges are produced either according to CIP for the civilian market or to order according to STANAG (9 mm NATO). For the cartridge, whose military designation is 5.56x45 mm NATO, STANAG does not specify parameters for the 55 grs round (or the M193 round was never introduced in NATO until the European SS109 round from Herstal). The manufacturer here follows the military standard where possible, but the cartridges are of course CIP compliant (there are related parameters that CIP does not address, such as waterproofing of the cartridges).
In the production exclusively for state customers there are also 5,56 x 45 mm NATO cartridges completely according to STANAG and with SS109 (M855) bullets, which STV is buying for the time being.
Currently, STV Technology employs 120 people, including management. Production runs in three shifts on weekdays and sometimes 12-hour shifts are added on weekends.
Milestones and future plans
In 2022, for the first time in history, STV Technology produced one hundred million rounds of 9mm Luger ammunition in one calendar year. In 2024, a new 5.56x45 mm cartridge with a proprietary SS109 bullet fully compliant with STANAG standards will be launched and a total of 260 million rounds of both calibers are planned to be produced in all production versions.
The first significant business milestone in the company's life was the introduction of a new trademark for all ammunition produced. In 2021, an entirely new brand, Scorpio, was created for all of the company's products. It is not only our shooters who are familiar with the scorpion emblem on the blue and silver consumable packaging.
In 2022, the delivery of machines for the production of 7.62x 39 mm FMJ and 7.62x 51 mm NATO M 80 rounds (including the civilian version 308 Winchester with 147 grs FMJ round) was contracted. The ordered equipment is expected to be delivered in phases in the second half of 2024, with full production ramping up in mid-2025. The 7.62 x 39 mm and 308 Win cartridges are primarily targeted at civilian customers in the US (and elsewhere), with 7.62 mm NATO customers expected to include ACR and allied military customers. An adjacent hall on the site has been selected for the production of 7,62 mm cartridges, but is in need of refurbishment. Establishing production on this scale is a very costly affair, but the company's quantitative goal is to produce up to five hundred million rounds per year, balancing production for both civilian and military customers. Another significant step forward was the establishment of Patriot Sports, a subsidiary based in Kansas, which has as its primary mission the distribution of ammunition produced by STV Technology in the US market. The latter is the dominant market for the company. In the middle of the year Patriot Sports engaged Alice Poluchova, former CEO of CZ-USA, first as director of new business projects and from September 2023 as manager. With her arrival, the Patriot Sports hub has reached the largest US distributors and is celebrating one sales success after another.
Production of 9 mm Luger cartridges
The production of 9 mm Luger cartridges was a logical choice right at the beginning, only about a year after the STV concern took control of the Poličské strojírny site. The first cartridges began to be produced in 2017 on machines purchased from Vlastimil Libra (whose dramatic business and human fate is quite well known to the Czech shooting public). These were single-purpose machines with an average age of 30 years or more. Just for the record, the oldest pieces of machinery were milling machines designed to machine cartridge cases into their final shape. These were made by the German company Fritz Werner as early as 1936 (and the company still exists today). Of course, these machines were not sufficient in capacity and precision for the current requirements.
The management of STV INVEST Holding considers the production of small-caliber bullets as one of its business priorities, which is why technological equipment from a first-class supplier, the Belgian company New Lachaussée, was purchased, installed and commissioned at the end of 2018. The single and multi-station progression presses of this manufacturer were supplemented by lathes from the Polish company Mesko, presses for inserting primers into cartridge cases from the American company Alpha Loading Systems, presses for filling and assembling cartridges from the domestic company Deimos and, finally, dressing machines from the Turkish company Ersan.
In 2023, another technological unit for the production of the 9 mm Luger cartridge was put into operation, this time assembled around multi-station progressive presses from the Italian company lnvernizzi. These machines were complemented by combined milling machines from the Italian manufacturer OMC Wire Lombardia, top Italian Vibron dressing machines and finally by products manufactured by STV's sister company DEUS Automation (presses for inserting the primer into the cartridge bed, presses for filling and assembling cartridges, packaging machines and optical inspection machines).
The combined production capacity of both technological systems is around 140 million rounds of 9 mm Luger ammunition in all production versions per year (calculated for a three-shift operation with an average number of 250 working days). The aim of this technological unit is to produce all major components in-house. With the exception of packaging materials, only energy components, i.e. matches and smokeless powder, are currently purchased from external suppliers. Metal components - cups for drawing the cartridge case and bullet jacket and lead semi-finished material for the production of bullet cores are preferentially purchased from European suppliers not only to ensure stable high quality but also to maintain the highest possible availability and speed of order fulfilment.
Production of pistol cartridges
For cartridge cases, the input material is a brass cup. It is drawn to the required length with a concave bottom by multi-station progressive presses. In the following operations, the bottom is pressed flat and the match bed is formed by punching the stopper. This is followed by the embossing of the bottom signature. The last machining operation is chip machining: the groove is sharpened, the edge of the bottom rim is knocked off and the cartridge case is shortened to the desired length. Between each production operation, the blank is always degreased, rinsed and dried. The last machine operation is followed by final degreasing, rinsing, pickling, passivation and polishing of the finished cartridge case. From this point on, the operator only wears gloves for all subsequent production operations. Fingers and hands leave undesirable visible marks on the surface of the brass parts.
Both the input cups and the individual stages of cartridge production are regularly and carefully checked after each production operation. In addition to dimensional inspection, the material composition, hardness, size and grain orientation of the material are verified with state-of-the-art instruments. Particularly specific are the inspections of the individual cuts, during which, among other things, the dimensional accuracy and the shape of the wall and bottom of the cartridge case are examined. The quality and accuracy of the individual stages and the finished cartridge are absolutely crucial for the production of a precise and reliable cartridge.
Production of 9 mm bullets
The 9 mm projectile consists of two parts: the core and the jacket. The core is made on single station presses by cutting and further forming wire, which is made of lead and antimony alloy. The core is then de-milled, rinsed and dried. It must still be ground to its final shape in order to fit flawlessly into the bullet assembly. I have seen for myself how precise the core production at STV Technology is. From the handling box where the die-cut cores fall directly from the press, I picked ten pieces at random and measured their weight on a digital scale that is part of the operator's control panel. I recorded a remarkable maximum deviation of ± 0.006 g for the cores transported, with a nominal core weight of 6.80 g and a maximum deviation of ± 0.1 g allowed.
The complete projectile is then produced on two-station progressive presses, where the cup of the projectile jacket is first pulled out and cut, into which the core is moulded. The core is dolly pressed by the machine so that it is homogeneously distributed, and the projectile shell is then tapered into its final shape. After this machining operation is completed, the projectile is degreased, rinsed, dried, pickled, passivated and polished by means of vibratory scrubbers. As is the case with the polished cartridge case, from the end of this operation onwards, the operator works in gloves only for all subsequent operations.
Again, I randomly selected ten finished shots, as they fell out of the press, to carry. For the reloaded bullets I recorded a maximum deviation of ± 0.008 g, with a nominal bullet weight of 8.0 g and a maximum deviation of ± 0.1 g allowed. As is the case with the cup designed for progressive case drawing, the bullet jacket cup is subjected to a rigorous initial inspection to verify dimensions, hardness, grain size and distribution, and section dimensions. The projectile itself is regularly checked both in terms of size and weight. STV Technology produces three types of 9 mm Luger bullets, two of which are FMJ (7.5 g/gr and 8.0 g/124 gr) and one type of TFMJ 8.0 g/124 gr. The TFMJ bullet differs from the conventional FMJ bullet in that the bottom of the bullet is covered by a brass slat that is encased by the bullet jacket. The lead core is thus completely enclosed in the jacket.
Assembly, inspection and packaging of pistol cartridges
The assembly of the cartridge is preceded by the technological operation of pressing the primer into the bed in the bottom of the cartridge case on machines from the American company Alpha Loading Systems and the Czech company DEUS Automation. After this operation, the position of the match in the bed, the depth and plane of its pressing in comparison with the bottom of the cartridge case are checked. The check is carried out using both manual calipers and high-speed cameras.
The actual filling of the hub and its assembly are carried out on machinery from the supplier DEUS Automation, which works on the principle of linear feeding of components between individual workstations.
The directed components are loaded into the machine, where the neck of the already fired cartridge is opened at the first position and at the next position a mass-controlled dose of powder is poured into the cartridge, which is subsequently checked by a laser beam (height of the powder level in the cartridge). At the next position, the projectile is inserted into the cartridge so that it is on the axis of the cartridge and at the prescribed depth. The next position is used to choke the neck of the cartridge case into the bullet body. The last position is an automatic check of the dimension of the assembled cartridge.
As can be seen, the machine performs a double check of the dust dose. In addition, the production control includes taking a specified number of samples after one hour of operation. These are examined for lift, accuracy of ejection charge weight (powder charge), bullet and cartridge weights, and any surface defects. The results of the checks are, of course, recorded. The same range of checks is always carried out after any stoppage of the machine, change of powder, primer or bullet type, or cartridge manufacture. The manufactured 9 x 19 mm NATO cartridge is subsequently sealed in the primer and case neck area to guarantee its watertightness.
Currently, STV Technology produces the following 9 mm caliber cartridges under the Scorpio or Patriot Sports brands: the 9 mm Luger FMJ 7.5 g, 9 mm Luger FMJ 8.0 g, 9 mm Luger TFMJ 8.0 g and 9 x 19 mm FMJ 8.0 g NATO.
Pistol cartridge check
Ballistic inspection is also part of the regular output inspection of the finished product. It is a set of tests measuring the lifting force, correctness of the labeling (checking the weight of powder in the bullet), checking the chamber pressure, bullet velocity at specified distances from the ballistic muzzle and bullet dispersion. In the case of the inspection of the military version of the 9 x 19 mm NATO cartridge, the product is tested according to a different methodology established by STANAG regulations.
The complete pre-packaging inspection of the product includes, in addition to the ballistic inspection, a check of the weight of the energetic component, verification of the bullet dimensions, its total weight and inspection of any surface defects.
An interesting figure disclosed by the company's representatives is the maximum allowable percentage of non-conforming products or components. The maximum permissible value in this case is 0.2% of all production operations.
The packaging of the finished products, which are released for final inspection, is carried out on robotic machines also supplied by our sister company DEUS Automation. Fifty cartridges are inserted into plastic insertion plates, which are then placed in paper consumer packaging.
Production of rifle cartridges
Apart from the Scorpio 9 mm Luger rounds that are already appearing in Czech shooting ranges, we were more curious about the production of 223 Remington / 5.56 x 45 mm NATO rifle rounds. These have only been on the market for a few months. We also tried them for the first time during a recent test of Steyr AUG rifles (loaned by our sister company STV Arms).
From the beginning, STV Technology has tried to manufacture as many hub components as possible in-house. The complete exception is matches and smokeless powder from reputable manufacturers from the USA, Germany and Bosnia and Herzegovina, for example. Cartridge cases and bullet casings are made by cold drawing from purchased brass cups. For the production of both metal components, it is determined that high and repeatable quality is maintained, especially the dimensions, material hardness, grain shape and direction. These input materials are purchased by STV Technology in the Czech Republic and Germany. The company has also tried brass components from non-European manufacturers, but unfortunately, Indian, Turkish or Chinese companies are not able to meet the requirements for balanced quality of individual supplies. In fact, the company plans to introduce its own production of cups. This will improve both quality and logistics. All other input materials, including oils, lubricants, coolants and replacement tools for individual machines, are procured by STV Technology from domestic suppliers.
The hubs are formed to the state when the signature is stamped on the bottom, the groove is sharpened and the neck is milled. In the meantime, they undergo neck annealing, several cleanings, degreasing, polishing and inspection. Projectiles identical to the M193 are formed from a lead core cut and shaped from lead wire, onto which is strung a jacket drawn from the cup. Alternatively, there is also the technology to produce totally sealed jacketed projectiles (TMJ), which in the 9 mm Luger calibre are created by adding and pressing a bottom cut from a copper sheet.
The assembly of 223 Rem cartridges is done on machines from DEUS Automation. The machines work with five rows of cartridges, so that one operation always modifies five cartridges. This can be followed by encapsulation, if required by the customer, and packing into boxes or cases. Then all that's left to do is carefully assemble and pack the pallets and the cartridges can go to their customers. By the way, a pallet here can hold 156,000 rounds of 223 Rem.
Production and output control
STV Technology takes great care to monitor and control the quality of individual parts, semi-finished and finished products.
The inspection system consists of an initial inspection, a regular operational inspection, a random production inspection and an output inspection, which includes ballistic testing.
During the production tour we were interested in checking the parameters of brass input material and parts in individual production nodes. In the laboratories, the composition of the materials, their hardness and, last but not least, the shape, size and orientation of the grains in the section are checked by means of a spectrometer using high-resolution microscopes. It goes without saying that all data are evaluated, recorded and archived.
The actual regular operational check of the specified parameters of the part or finished product is carried out by the operators of individual machines at regular intervals from a defined number of samples. Random production inspection is carried out by the inspection department personnel at prescribed intervals and in defined quantities. The results of the checks are recorded and immediately evaluated. In the event of any non-conformity, the production operation is interrupted, the machine is adjusted and the quantity produced since the last positive check is evaluated piecewise.
At the filling press and hub assembly, I was present for the regular inspection of the manufactured hub. Every hour a sample of 10 bullets is taken, for which the lift force is measured, the accuracy of smokeless powder loading, the weight of the bullet and cartridge case, and the weight of the whole bullet are measured and evaluated. A total of 80 cartridges of any lead or bore are checked in this way in any one production shift.
Although opto-electric sorting machines are used for operational, production and other inspections of non-conforming pieces, the human eye still has an irreplaceable role in the random inspection of surface defects in the hub. As proof of the output inspection, the production batch number, date of manufacture and personal number of the inspector who released the cartridge for sale are printed on the closing flap of the consumer package.
STV Technology is ISO 9001:2015 and 14001:2015 certified. In 2024 they are also going to obtain AQAP 2110 certification, which is necessary for supplying ammunition to armed forces not only in NATO member countries.
Conclusion
STV Technology started producing cartridges relatively recently, but they understood that even though 9 mm Luger and 223 Rem / 5.56 x 45 mm cartridges are by their nature a commodity where the price of the product is the determining sales criterion, without top quality or at least solid quality it is impossible to achieve success in demanding markets.
At the cost of considerable investments, the STV holding built a modern production of bullets on the Polička site. The production and its individual stages are constantly being improved and the machinery is gradually being replaced to achieve high production figures with the same or increasing quality. Most of the cartridges produced here go for export, but they can be found without any problems in the Czech Republic, mainly in the shops of our sister company STV Arms or at shooting ranges all over the Czech Republic.
Representatives of STV Technology told us that their cartridges, thanks to their quality, can withstand repeated reloading. We'll probably try it ourselves.