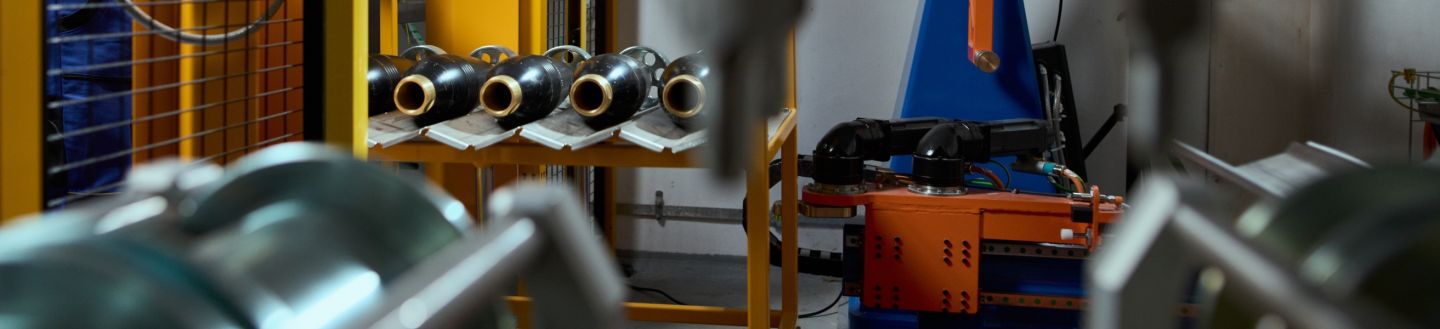
The launch of a new line for filling (not only) artillery shells is the beginning of a new era for STV GROUP
STV GROUP is preparing for a new era of production of 155mm ammunition for NATO guns at its plant in Polička. Recently, it has therefore invested mainly in the development of large-calibre ammunition production. This year, for example, the company commissioned a new line for filling artillery shells with explosives.
CZDEFENCE magazine in its December issue brought a report from the production of large-calibre ammunition in STV GROUP.
STV GROUP is preparing for a new era of production of 155mm ammunition for NATO guns at its plant in Polička. It has therefore recently invested in the development of large-calibre ammunition production. This year, for example, the company put into operation a new line for filling artillery shells with explosives, purchasing the SA-15 single-spindle auger automatic machine from the leading European manufacturer Konstrukta Industry. This is the latest generation of large-calibre ammunition filling machines. Moreover, Konstrukta is the only manufacturer of this type of machine that exports to many countries.
Screw extrusion or screw extrusion is a highly efficient filling technology for artillery, tank or mortar ammunition. This method is carried out with a hot screw and is based on continuous pressing of the explosive, layer by layer, inside the casing cavity. The processed material retains its primary properties, which are an essential requirement for ensuring the consistent quality of the explosive charge. This technology, compared to casting molten explosive, reduces the risk of so-called lunkers, i.e. gaps and bubbles in the explosive as it solidifies. In addition, it is a faster and less energy-intensive method of filling compared to the laboratory casting technology.
We were interested in the advantages of the SA-15 machine, so we asked the production manager of STV GROUP Ing. Martin Novotny, who told us that it is mainly very efficient and short filling time. The screw extrusion filling machine is located in a bunker and operates without the presence of an operator to ensure a high level of operational safety. In Polička, the "dungeon" in which the machine is located has reinforced concrete walls two and a half metres wide and must withstand the explosion of a grenade body. Due to the temperature of the whole process (about 60 degrees), the state of the explosive charge immediately after the filling process allows further operations to continue. Quality control by X-ray system is also not required. This method uses split bodies for quality control and has a specific structure that is not prone to defects such as bubbles, cracks or other quality defects. It is not necessary to change the state of the explosive from solid to liquid phase and vice versa. The production process is continuous, so that it is not necessary to collect large quantities of filled grenade bodies in the production area.
The whole process of filling the grenade takes place in the space of a single hall. At one end, workers tie up the prepared bodies of ammunition for gentle heating to the exact temperature, and through the process of augering and subsequent cleaning of the ignition compartment and the painting process at the end of the same compartment, the grenades leave the hall without the igniter. The grenades are filled with TNT in a solid state, which also undergoes minimal heating. Thanks to the house, the substance is able to form a homogeneous solid unit. The filling machine is versatile and, with a short change of input parameters and auger size adjustment, allows filling ammunition in calibers from 76 mm to 155 mm. We were able to see the entire production process in person and with a camera. The advantages of the machine also include relatively low energy costs and the possibility of operation by a small team of employees.
The entire production process is accompanied by strict safety conditions and necessary maintenance. The quality control of the TNT screw is carried out by means of split bodies and, after disassembly, by cutting the filling to reveal even the smallest manufacturing defects. At present, the machine fills artillery shells of 122 mm calibre, and as we have already mentioned earlier, it is ready to start filling 155 mm ammunition for NATO guns. The technology is also adapted to fill artillery ammunition with extended range. The total production capacity of the line, depending on the calibre of the ammunition, is 56,000-150,000 pieces per year.
We asked David Hac, Chairman of the Board of Directors of STV GROUP, what the company expects from the launch of the new artillery shell filling line. This means that we are now really starting to have the capability to produce ammunition from 81 millimetre calibre up to 155 millimetre calibre." At the same time, David Hác adds that the transition to the new SA-15 machine was quite easy because the company already had experience with the SA type. We had the SH-8, which was designed for 120 millimetre mortar shells of the Russian type. We also used it for 125 mm and 152 mm calibre ammunition." According to the chairman of the board of STV GROUP, augering is a technology that has proven itself.
The future ambition of the Polička plant is to switch to the 155mm NATO calibre. However, as we could see on site, the line is already producing 122 mm calibre. "As for the near future, after the production of 122 mm ammunition is finished, the line will start producing 81 mm and 120 mm mines for the Czech Army. These are mines for the Expal mortar. And then in about January or February next year it will start production of 155 mm ammunition for which is currently high world-wide demand. Later we will start preparing the ammunition for certification and after the certification is completed and the Caesar guns are delivered to the Czech army, we will start serial production of this ammunition for the Czech Army," David Hác revealed his future plans.
The STV Group also tries to participate in programmes announced by the European Commission. "We participated in the Track 2 programme, where the requirement was to supply millions of 155 millimetre calibre ammunition. However, we were not awarded a contract there," Hác revealed, adding that the commission had awarded a total of eight contracts, mostly to companies from large Western countries such as France and Germany. "However, now there is a call, which is called Track 3 or ASAP (Act in Support of Ammunition Production, n.d.). We are planning to enter some of our projects to expand the production of large-volume ammunition and it will concern 155 millimetre ammunition as well as other types of ammunition," says David Hác, Chairman of the Board of STV GROUP, who says: "We are definitely planning to purchase another similar line SA-15 in order to have redundant technology and sufficient capacity."